Essential Palletizer
Line Series
Increase efficiency, enhance productivity, and improve throughput with our robotic palletizers and depalletizers. Designed for our customer’s desired speed, service life, payload, reach, repeatability, and affordability, our palletizing and depalletizing automation systems can be integrated for any application. Simplimatic’s Essential Palletizer Line feature four different, highly cost-effective, and compact palletizers and depalletizers.
Download Essential Palletizer Line Specs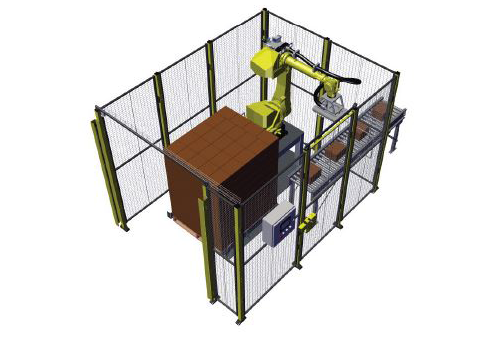
Compact
Reduce floorspace, offering a single pallet station with manual load/unload functionality.
Speed: Up to 12 cases per minute
Minimum Case Size: 9″ (L) x 5″ (W) x 6″ (H) up to 40 lbs.
Maximum Case Size: 17.5″ (L) x 15″ (W) x 20″ (H) up to 40 lbs
Operation: Robotic
Software: Simply Load, our custom pallet configuration tool, enables users to visualize, edit, implement and manage patterns on the HMI.
Machine Size Range (ft):
10.3 (L) x 7.5 (W) x 8.3 (H)
Controls: Turck*
PackML Compliant
PanelView Color HMI
Pneumatics: 80 psi
Voltage: 460 VAC
Disconnect: 30 Amps
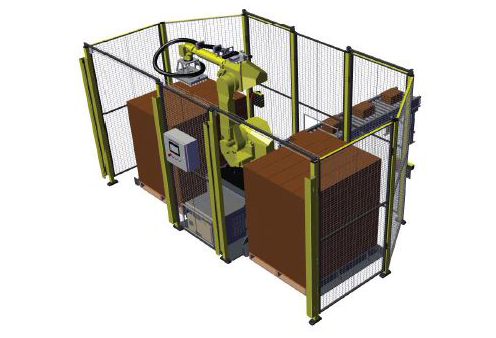
Dual
Expand your work station for continuous operation while maintaining manual load/unload functionality.
Speed: Up to 12 cases per minute
Minimum Case Size: 9″ (L) x 5″ (W) x 6″ (H) up to 40 lbs.
Maximum Case Size: 17.5″ (L) x 15″ (W) x 20″ (H) up to 40 lbs
Operation: Robotic
Software: Simply Load, our custom pallet configuration tool, enables users to visualize, edit, implement and manage patterns on the HMI.
Machine Size Range (ft):
12 (L) x 8.9 (W) x 7.6 (H)
Controls: Turck*
PackML Compliant
PanelView Color HMI
Pneumatics: 80 psi
Voltage: 460 VAC
Disconnect: 30 Amps
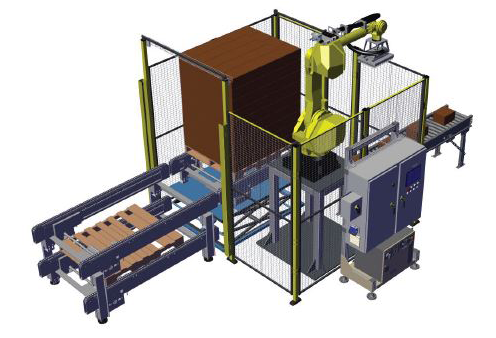
Over/Under
Offering dual pallet conveyor, this solution provides continuous operations without manual interface.
Speed: Up to 12 cases per minute
Minimum Case Size: 9″ (L) x 5″ (W) x 6″ (H) up to 40 lbs.
Maximum Case Size: 17.5″ (L) x 15″ (W) x 20″ (H) up to 40 lbs
Operation: Robotic
Software: Simply Load, our custom pallet configuration tool, enables users to visualize, edit, implement and manage patterns on the HMI.
Machine Size Range (ft):
15 (L) x 9 (W) x 11 (H)
Controls: Turck*
PackML Compliant
PanelView Color HMI
Pneumatics: 80 psi
Voltage: 460 VAC
Disconnect: 30 Amps
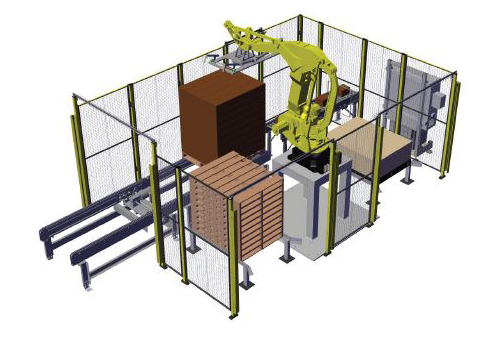
Pallet Handling
Provides automatic slip sheet handling in addition to the pallet load and discharge functions.
Speed: Up to 12 cases per minute
Minimum Case Size: 9″ (L) x 5″ (W) x 6″ (H) up to 40 lbs.
Maximum Case Size: 17.5″ (L) x 15″ (W) x 20″ (H) up to 40 lbs
Operation: Robotic
Software: Simply Load, our custom pallet configuration tool, enables users to visualize, edit, implement and manage patterns on the HMI.
Machine Size Range (ft):
20 (L) x 11 (W) x 8.5 (H)
Controls: Turck*
PackML Compliant
PanelView Color HMI
Pneumatics: 80 psi
Voltage: 460 VAC
Disconnect: 30 Amps